Budowa maszyn roboczych to złożony proces, który wymaga zrozumienia wielu kluczowych elementów. W każdej maszynie roboczej można wyróżnić kilka podstawowych komponentów, które współdziałają ze sobą, aby zapewnić efektywne działanie. Do najważniejszych z nich należy zaliczyć napęd, który może być mechaniczny lub elektryczny. Napęd jest odpowiedzialny za generowanie ruchu, który jest niezbędny do wykonywania określonych zadań. Kolejnym istotnym elementem jest układ sterujący, który pozwala na precyzyjne zarządzanie pracą maszyny. W nowoczesnych maszynach roboczych często stosuje się systemy automatyzacji, które zwiększają wydajność i dokładność operacji. Oprócz tego ważnym aspektem jest konstrukcja nośna, która musi być wystarczająco wytrzymała, aby unieść wszystkie pozostałe elementy oraz obciążenia podczas pracy. Nie można zapomnieć o układzie hydrauliki lub pneumatyki, które są kluczowe w wielu maszynach roboczych, umożliwiając przenoszenie dużych sił przy minimalnym zużyciu energii.
Jakie są najpopularniejsze rodzaje maszyn roboczych
W kontekście budowy maszyn roboczych warto zwrócić uwagę na różnorodność ich typów oraz zastosowań. Istnieje wiele rodzajów maszyn roboczych, które różnią się między sobą przeznaczeniem oraz sposobem działania. Do najpopularniejszych należą maszyny budowlane, takie jak koparki, ładowarki czy dźwigi, które są niezbędne w pracach ziemnych i budowlanych. Innym ważnym segmentem są maszyny przemysłowe, które obejmują urządzenia takie jak prasy, tokarki czy frezarki. Te maszyny służą do obróbki materiałów i produkcji różnorodnych komponentów. W rolnictwie natomiast dominują maszyny takie jak ciągniki, kombajny czy siewniki, które znacznie ułatwiają prace polowe i zwiększają wydajność produkcji rolniczej. Warto również wspomnieć o maszynach transportowych, takich jak wózki widłowe czy podnośniki, które są niezbędne w logistyce i magazynowaniu.
Jakie technologie są wykorzystywane w budowie maszyn roboczych
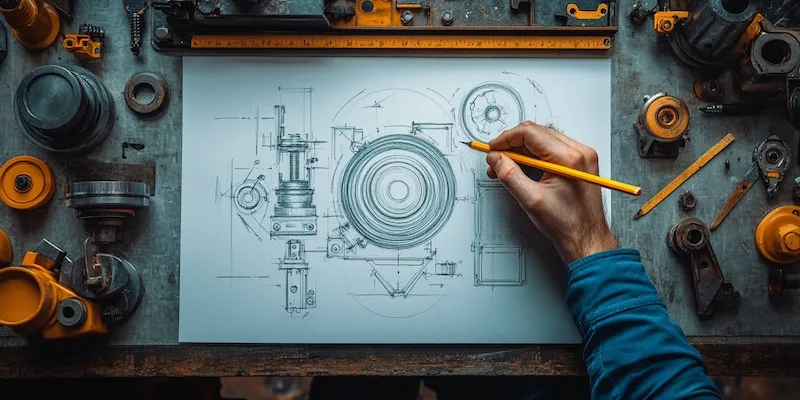
W dzisiejszych czasach budowa maszyn roboczych opiera się na zaawansowanych technologiach, które znacząco wpływają na ich wydajność i funkcjonalność. Jednym z kluczowych trendów jest zastosowanie technologii cyfrowych oraz automatyzacji procesów produkcyjnych. Dzięki temu możliwe jest precyzyjne projektowanie komponentów za pomocą programów CAD oraz symulacje ich działania w rzeczywistych warunkach. Wiele nowoczesnych maszyn roboczych wyposażonych jest w systemy monitorowania i diagnostyki, co pozwala na bieżąco śledzić ich stan techniczny oraz przewidywać ewentualne awarie. Kolejnym istotnym aspektem jest wykorzystanie materiałów kompozytowych oraz lekkich stopów metali, które pozwalają na redukcję masy maszyny przy jednoczesnym zachowaniu wysokiej wytrzymałości. Technologia napędu elektrycznego staje się coraz bardziej popularna wśród producentów maszyn roboczych ze względu na jej efektywność energetyczną oraz mniejszy wpływ na środowisko naturalne. Również rozwój technologii związanych z robotyką i sztuczną inteligencją otwiera nowe możliwości w zakresie automatyzacji procesów i zwiększenia precyzji działań maszyn roboczych.
Jakie są wyzwania związane z budową maszyn roboczych
Budowa maszyn roboczych wiąże się z wieloma wyzwaniami, które mogą wpływać na cały proces projektowania i produkcji. Jednym z głównych problemów jest konieczność dostosowania się do szybko zmieniających się wymagań rynku oraz oczekiwań klientów. W miarę jak technologia ewoluuje, producenci muszą stale aktualizować swoje rozwiązania i wprowadzać innowacje, aby utrzymać konkurencyjność. Kolejnym wyzwaniem są kwestie związane z bezpieczeństwem użytkowników oraz ochroną środowiska. Maszyny robocze powinny spełniać rygorystyczne normy dotyczące emisji spalin oraz hałasu, co wymaga zastosowania nowoczesnych technologii i materiałów. Dodatkowo producenci muszą zmierzyć się z problemami logistycznymi związanymi z dostawami komponentów oraz surowców do produkcji. W kontekście globalizacji łańcuchy dostaw stają się coraz bardziej skomplikowane i wymagają efektywnego zarządzania. Nie można również zapominać o konieczności szkolenia pracowników obsługujących te maszyny oraz zapewnienia im odpowiednich warunków pracy.
Jakie są kluczowe aspekty projektowania maszyn roboczych
Projektowanie maszyn roboczych to proces, który wymaga uwzględnienia wielu kluczowych aspektów, aby zapewnić ich efektywność oraz bezpieczeństwo użytkowania. Przede wszystkim, istotne jest zrozumienie specyfikacji technicznych oraz wymagań dotyczących wydajności, które maszyna ma spełniać. W tym kontekście ważne jest przeprowadzenie analizy potrzeb użytkowników oraz warunków, w jakich maszyna będzie pracować. Kolejnym krokiem jest dobór odpowiednich materiałów, które muszą charakteryzować się wysoką wytrzymałością oraz odpornością na różnorodne czynniki zewnętrzne, takie jak korozja czy wysokie temperatury. Projektanci muszą również zwrócić uwagę na ergonomię urządzenia, aby zapewnić komfort i bezpieczeństwo operatora. Oprócz tego istotne jest uwzględnienie aspektów związanych z konserwacją i serwisowaniem maszyny, co pozwoli na dłuższe jej użytkowanie oraz minimalizację przestojów. Warto także pamiętać o integracji nowoczesnych technologii, takich jak systemy monitorowania czy automatyzacja procesów, które mogą znacząco zwiększyć efektywność pracy maszyny.
Jakie są najnowsze trendy w budowie maszyn roboczych
W ostatnich latach budowa maszyn roboczych uległa znacznym zmianom, a nowe trendy kształtują przyszłość tej branży. Jednym z najważniejszych kierunków rozwoju jest automatyzacja procesów produkcyjnych oraz wprowadzenie sztucznej inteligencji do działania maszyn. Dzięki tym technologiom możliwe jest zwiększenie precyzji operacji oraz redukcja błędów ludzkich. Wiele firm inwestuje w rozwój robotów przemysłowych, które mogą wykonywać skomplikowane zadania w sposób szybki i efektywny. Kolejnym trendem jest rosnąca popularność maszyn elektrycznych, które są bardziej ekologiczne i oszczędne w eksploatacji niż tradycyjne maszyny spalinowe. W odpowiedzi na rosnące wymagania dotyczące ochrony środowiska producenci starają się wprowadzać rozwiązania zmniejszające emisję spalin oraz hałas podczas pracy maszyn. Również rozwój technologii 3D druku staje się coraz bardziej powszechny w budowie maszyn roboczych, umożliwiając szybsze prototypowanie i produkcję komponentów o skomplikowanych kształtach. Innowacje te mają na celu nie tylko poprawę wydajności maszyn, ale także ich dostosowanie do indywidualnych potrzeb klientów oraz specyfiki różnych branż przemysłowych.
Jakie są kluczowe czynniki wpływające na trwałość maszyn roboczych
Trwałość maszyn roboczych to jeden z najważniejszych aspektów ich eksploatacji, który wpływa na koszty utrzymania oraz efektywność pracy. Kluczowym czynnikiem determinującym trwałość maszyny jest jakość zastosowanych materiałów oraz komponentów. Wysokiej jakości stal czy tworzywa sztuczne mogą znacznie wydłużyć żywotność urządzenia i zmniejszyć ryzyko awarii. Kolejnym istotnym elementem jest regularna konserwacja i serwisowanie maszyny, co pozwala na bieżąco monitorować jej stan techniczny oraz wykrywać potencjalne problemy zanim przerodzą się one w poważne usterki. Ważne jest także przestrzeganie zaleceń producenta dotyczących użytkowania maszyny oraz jej obciążenia – przeciążenie może prowadzić do szybszego zużycia komponentów i skrócenia żywotności urządzenia. Oprócz tego warto zwrócić uwagę na warunki pracy maszyny; ekstremalne temperatury, wilgotność czy obecność substancji chemicznych mogą negatywnie wpłynąć na jej trwałość.
Jakie są metody testowania maszyn roboczych przed ich wdrożeniem
Testowanie maszyn roboczych przed ich wdrożeniem to kluczowy etap procesu produkcji, który ma na celu zapewnienie ich niezawodności oraz bezpieczeństwa użytkowania. Istnieje wiele metod testowania, które można zastosować w zależności od rodzaju maszyny oraz jej przeznaczenia. Jedną z podstawowych metod jest testowanie funkcjonalne, które polega na sprawdzeniu wszystkich funkcji maszyny w rzeczywistych warunkach pracy. Dzięki temu można zweryfikować, czy urządzenie spełnia określone normy wydajnościowe i jakościowe. Kolejnym krokiem są testy obciążeniowe, które mają na celu sprawdzenie wytrzymałości komponentów pod dużymi obciążeniami oraz ich odporności na uszkodzenia mechaniczne. Testy te pomagają również ocenić reakcję maszyny na różnorodne warunki pracy. Ważnym elementem procesu testowania są również analizy bezpieczeństwa, które mają na celu identyfikację potencjalnych zagrożeń dla operatora oraz otoczenia podczas eksploatacji maszyny. W przypadku nowoczesnych rozwiązań technologicznych często stosuje się symulacje komputerowe, które pozwalają na przewidzenie zachowań maszyny w różnych scenariuszach bez konieczności przeprowadzania kosztownych testów fizycznych.
Jakie są koszty związane z budową maszyn roboczych
Koszty związane z budową maszyn roboczych mogą być bardzo zróżnicowane i zależą od wielu czynników, takich jak typ maszyny, zastosowane technologie czy materiały użyte do produkcji. Na początku należy uwzględnić koszty projektowania i inżynieryjnych prac badawczo-rozwojowych, które mogą być znaczące zwłaszcza przy tworzeniu innowacyjnych rozwiązań technologicznych. Następnie pojawiają się koszty zakupu surowców i komponentów niezbędnych do produkcji maszyny; ceny tych materiałów mogą się różnić w zależności od jakości oraz dostawcy. Kolejnym istotnym elementem są koszty produkcji związane z wynagrodzeniami pracowników oraz utrzymaniem infrastruktury produkcyjnej. Po zakończeniu procesu budowy należy również uwzględnić koszty testowania i certyfikacji maszyny przed jej wdrożeniem do użytku komercyjnego. Dodatkowo warto pamiętać o kosztach związanych z późniejszym serwisowaniem i konserwacją urządzenia przez cały okres jego eksploatacji; regularne przeglądy mogą znacząco wpłynąć na jego trwałość oraz efektywność działania.
Jakie są przyszłe kierunki rozwoju branży budowy maszyn roboczych
Przemysł budowy maszyn roboczych stoi przed wieloma wyzwaniami i możliwościami rozwoju w nadchodzących latach. Zmiany technologiczne oraz rosnące wymagania rynku będą miały kluczowy wpływ na przyszłość tej branży. Jednym z głównych kierunków rozwoju będzie dalsza automatyzacja procesów produkcyjnych oraz integracja sztucznej inteligencji w działaniu maszyn roboczych. Dzięki tym rozwiązaniom możliwe będzie zwiększenie wydajności pracy oraz redukcja błędów ludzkich podczas obsługi urządzeń. Kolejnym ważnym trendem będzie rosnąca potrzeba dostosowywania maszyn do indywidualnych potrzeb klientów; producenci będą musieli oferować elastyczne rozwiązania umożliwiające personalizację produktów zgodnie z wymaganiami rynku.