Przemysł 4.0 to termin, który odnosi się do czwartej rewolucji przemysłowej, charakteryzującej się integracją nowoczesnych technologii w procesach produkcyjnych. W odróżnieniu od poprzednich rewolucji, które skupiały się głównie na mechanizacji i automatyzacji, przemysł 4.0 wprowadza koncepcje takie jak Internet Rzeczy (IoT), sztuczna inteligencja oraz analityka danych w czasie rzeczywistym. Te innowacje pozwalają na bardziej elastyczne i zautomatyzowane procesy produkcyjne, co prowadzi do zwiększenia efektywności oraz redukcji kosztów. W praktyce oznacza to, że maszyny mogą komunikować się ze sobą oraz z systemami zarządzania, co umożliwia szybsze podejmowanie decyzji i lepsze dostosowywanie produkcji do zmieniających się potrzeb rynku.
Jakie technologie są kluczowe dla przemysłu 4.0?
W kontekście przemysłu 4.0 istnieje wiele technologii, które odgrywają kluczową rolę w transformacji procesów produkcyjnych. Jedną z najważniejszych jest Internet Rzeczy (IoT), który pozwala na podłączenie maszyn i urządzeń do sieci, umożliwiając ich zdalne monitorowanie oraz zarządzanie. Dzięki IoT możliwe jest zbieranie danych w czasie rzeczywistym, co pozwala na bieżąco analizowanie wydajności produkcji oraz identyfikowanie potencjalnych problemów. Kolejną istotną technologią jest sztuczna inteligencja, która umożliwia automatyzację procesów decyzyjnych oraz optymalizację działań produkcyjnych. Analiza dużych zbiorów danych pozwala na przewidywanie trendów rynkowych oraz dostosowywanie strategii produkcji do zmieniających się warunków.
Jakie korzyści przynosi wdrożenie przemysłu 4.0?
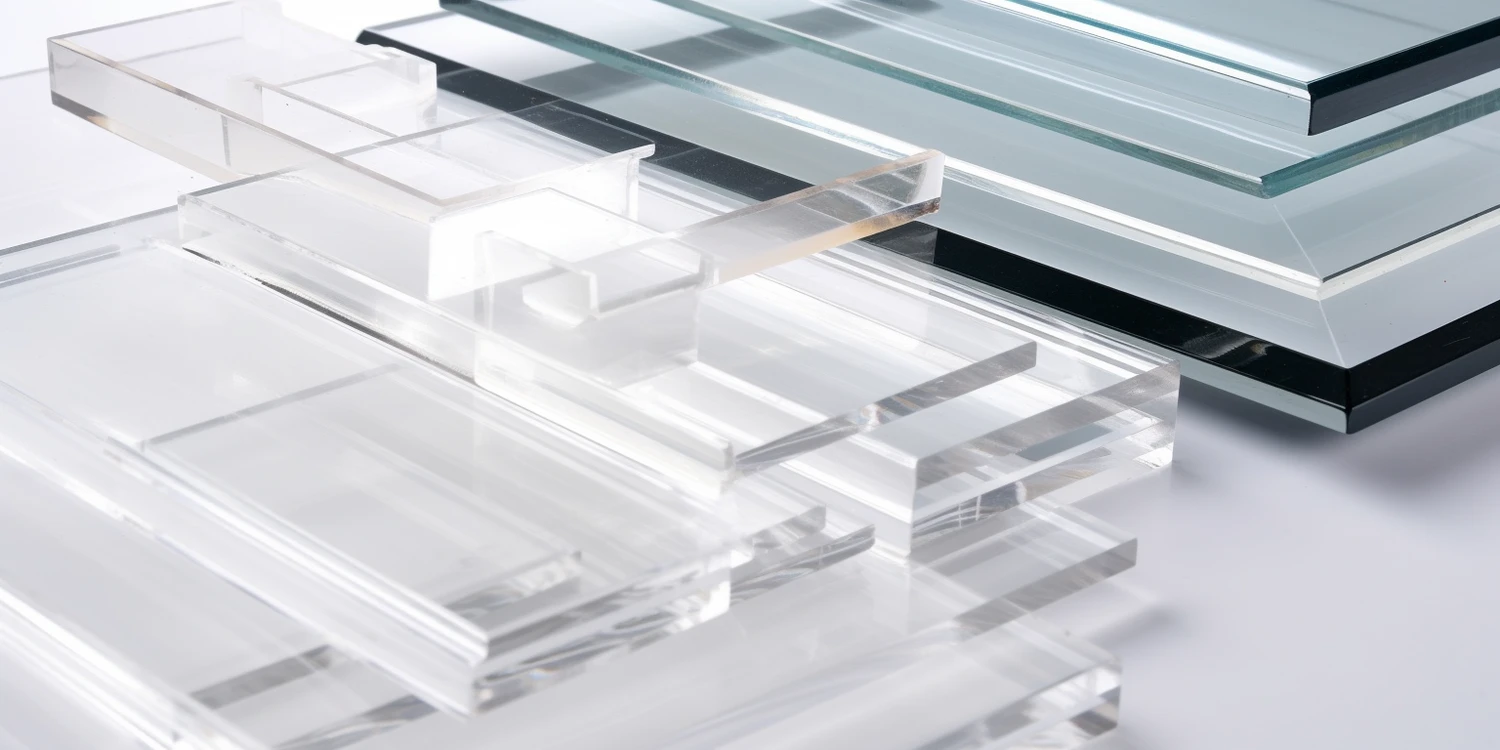
Wdrożenie koncepcji przemysłu 4.0 przynosi wiele korzyści zarówno dla przedsiębiorstw, jak i dla całej gospodarki. Przede wszystkim zwiększa efektywność procesów produkcyjnych poprzez automatyzację i optymalizację działań, co prowadzi do obniżenia kosztów operacyjnych. Dzięki zastosowaniu nowoczesnych technologii możliwe jest także szybsze reagowanie na zmiany popytu oraz lepsze dostosowywanie oferty do potrzeb klientów. W rezultacie firmy mogą osiągnąć wyższą konkurencyjność na rynku oraz zwiększyć swoją rentowność. Ponadto przemysł 4.0 przyczynia się do poprawy jakości produktów poprzez ciągłe monitorowanie procesów i eliminowanie błędów już na etapie produkcji.
Jakie wyzwania wiążą się z przemysłem 4.0?
Pomimo licznych korzyści związanych z wdrożeniem przemysłu 4.0 istnieją także istotne wyzwania, które przedsiębiorstwa muszą pokonać, aby skutecznie zaimplementować nowe technologie. Jednym z głównych problemów jest konieczność inwestycji w infrastrukturę technologiczną oraz szkolenia pracowników, co może być kosztowne i czasochłonne. Firmy muszą również zmierzyć się z kwestiami związanymi z bezpieczeństwem danych oraz ochroną prywatności, ponieważ gromadzenie dużych ilości informacji wiąże się z ryzykiem ich nieautoryzowanego dostępu lub wykorzystania. Dodatkowo organizacje muszą radzić sobie z oporem ze strony pracowników, którzy mogą obawiać się utraty pracy lub konieczności przystosowania się do nowych warunków pracy.
Jakie są przykłady zastosowania przemysłu 4.0 w praktyce?
Przykłady zastosowania przemysłu 4.0 można znaleźć w wielu branżach, które z powodzeniem wdrażają nowoczesne technologie w swoich procesach produkcyjnych. W przemyśle motoryzacyjnym wiele firm korzysta z robotów współpracujących, które pracują obok ludzi na liniach montażowych, co zwiększa wydajność i bezpieczeństwo pracy. Dzięki zastosowaniu systemów IoT, producenci mogą monitorować stan maszyn w czasie rzeczywistym, co pozwala na przewidywanie awarii i planowanie konserwacji zanim dojdzie do przestojów. W branży spożywczej technologia blockchain jest wykorzystywana do śledzenia pochodzenia produktów oraz zapewnienia ich jakości, co jest szczególnie istotne w kontekście rosnących wymagań konsumentów dotyczących transparentności. Z kolei w sektorze energetycznym inteligentne sieci energetyczne umożliwiają zarządzanie dostawami energii oraz optymalizację zużycia, co przyczynia się do efektywności energetycznej i redukcji kosztów.
Jakie umiejętności są potrzebne w erze przemysłu 4.0?
W erze przemysłu 4.0 zmieniają się wymagania dotyczące umiejętności pracowników, co stawia przed nimi nowe wyzwania. Kluczowe stają się kompetencje związane z obsługą nowoczesnych technologii, takich jak programowanie robotów, analiza danych czy zarządzanie systemami IoT. Pracownicy powinni być także otwarci na ciągłe uczenie się i adaptację do zmieniającego się środowiska pracy, ponieważ technologie rozwijają się w szybkim tempie. Umiejętności miękkie, takie jak zdolność do pracy zespołowej, komunikacja oraz kreatywność, również nabierają znaczenia, ponieważ współpraca między ludźmi a maszynami staje się coraz bardziej powszechna. Warto również zwrócić uwagę na znaczenie umiejętności analitycznych, które pozwalają pracownikom na interpretację danych i podejmowanie decyzji opartych na faktach.
Jakie są perspektywy rozwoju przemysłu 4.0 w przyszłości?
Perspektywy rozwoju przemysłu 4.0 są obiecujące i wskazują na dalszy wzrost znaczenia nowoczesnych technologii w procesach produkcyjnych. W miarę jak technologia będzie się rozwijać, możemy spodziewać się jeszcze większej automatyzacji oraz integracji systemów produkcyjnych z innymi obszarami działalności przedsiębiorstw. Sztuczna inteligencja będzie odgrywać kluczową rolę w podejmowaniu decyzji oraz optymalizacji procesów, a rozwój technologii takich jak uczenie maszynowe pozwoli na jeszcze lepsze przewidywanie trendów rynkowych oraz dostosowywanie produkcji do potrzeb klientów. Warto również zauważyć rosnące zainteresowanie zrównoważonym rozwojem i ekologicznymi rozwiązaniami, co może wpłynąć na kierunki innowacji w przemyśle 4.0. Firmy będą coraz częściej poszukiwać sposobów na minimalizację wpływu swojej działalności na środowisko oraz zwiększenie efektywności energetycznej.
Jakie są różnice między przemysłem 4.0 a wcześniejszymi rewolucjami przemysłowymi?
Różnice między przemysłem 4.0 a wcześniejszymi rewolucjami przemysłowymi są znaczące i dotyczą zarówno technologii, jak i podejścia do produkcji. Pierwsza rewolucja przemysłowa skoncentrowana była głównie na mechanizacji procesów produkcyjnych za pomocą maszyn parowych, co prowadziło do zwiększenia wydajności pracy manualnej. Druga rewolucja przyniosła elektryczność oraz liniową produkcję masową, co umożliwiło dalszą automatyzację i standaryzację procesów. Trzecia rewolucja to era cyfryzacji, która wprowadziła komputery i automatyzację procesów za pomocą technologii informacyjnych. Przemysł 4.0 natomiast opiera się na integracji wszystkich tych elementów z nowoczesnymi technologiami takimi jak IoT czy sztuczna inteligencja, co pozwala na stworzenie inteligentnych fabryk zdolnych do samodzielnego podejmowania decyzji oraz adaptacji do zmieniających się warunków rynkowych.
Jakie są najważniejsze trendy związane z przemysłem 4.0?
W kontekście przemysłu 4.0 można zaobserwować kilka kluczowych trendów, które mają istotny wpływ na przyszłość produkcji i zarządzania przedsiębiorstwami. Jednym z nich jest rosnąca popularność sztucznej inteligencji oraz uczenia maszynowego, które pozwalają na automatyzację procesów decyzyjnych oraz przewidywanie trendów rynkowych na podstawie analizy danych historycznych. Kolejnym ważnym trendem jest rozwój Internetu Rzeczy (IoT), który umożliwia podłączenie maszyn i urządzeń do sieci oraz zbieranie danych w czasie rzeczywistym, co przekłada się na lepsze zarządzanie procesami produkcyjnymi. Wzrasta także znaczenie cyberbezpieczeństwa, ponieważ rosnąca liczba połączonych urządzeń stwarza nowe zagrożenia dla danych i systemów informatycznych przedsiębiorstw.
Jakie są kluczowe czynniki sukcesu przy wdrażaniu przemysłu 4.0?
Aby skutecznie wdrożyć koncepcję przemysłu 4.0, przedsiębiorstwa muszą zwrócić uwagę na kilka kluczowych czynników sukcesu. Po pierwsze istotne jest zaangażowanie najwyższego kierownictwa w proces transformacji oraz stworzenie wizji długoterminowej strategii rozwoju opartej na nowoczesnych technologiach. Kolejnym ważnym elementem jest inwestycja w odpowiednią infrastrukturę technologiczną oraz szkolenia dla pracowników, aby zapewnić im niezbędne umiejętności do obsługi nowych systemów i narzędzi. Ważne jest także stworzenie kultury innowacji wewnątrz organizacji, która sprzyjać będzie eksperymentowaniu oraz wdrażaniu nowych pomysłów bez obaw przed porażką.