Destylacja rozpuszczalników to proces, który polega na oddzieleniu składników mieszaniny na podstawie różnicy w ich temperaturach wrzenia. Jest to technika szeroko stosowana w chemii, przemyśle farmaceutycznym oraz w produkcji napojów alkoholowych. W procesie tym najpierw podgrzewa się ciecz, co powoduje jej parowanie. Następnie para jest schładzana i skraplana, co pozwala na uzyskanie czystego rozpuszczalnika. Kluczowym elementem jest dobór odpowiednich warunków, takich jak temperatura i ciśnienie, które wpływają na efektywność destylacji. W przypadku rozpuszczalników organicznych, takich jak etanol czy aceton, ważne jest również uwzględnienie ich właściwości chemicznych oraz ewentualnych reakcji zachodzących podczas procesu. Destylacja może być przeprowadzana w różnych układach, w tym w kolumnach destylacyjnych, które umożliwiają wielokrotne skraplanie i parowanie, co zwiększa czystość uzyskanego produktu.
Jakie są najczęściej stosowane metody destylacji rozpuszczalników
W dziedzinie destylacji rozpuszczalników wyróżnia się kilka metod, które są dostosowane do specyficznych potrzeb i właściwości substancji. Najpopularniejszą z nich jest destylacja prosta, która znajduje zastosowanie przy separacji składników o znacznej różnicy temperatur wrzenia. Ta metoda jest stosunkowo łatwa do przeprowadzenia i nie wymaga zaawansowanego sprzętu. Kolejną metodą jest destylacja frakcyjna, która umożliwia oddzielanie składników o zbliżonych temperaturach wrzenia poprzez wielokrotne skraplanie i parowanie. W przypadku bardziej skomplikowanych mieszanin warto zastosować destylację azeotropową, która pozwala na usunięcie składników tworzących azeotropy, czyli mieszaniny o stałym składzie. Oprócz tych klasycznych metod istnieją także nowoczesne techniki, takie jak destylacja membranowa czy destylacja podciśnieniowa, które oferują dodatkowe korzyści, takie jak niższe temperatury procesowe czy oszczędność energii.
Jakie są zalety i wady stosowania destylacji rozpuszczalników
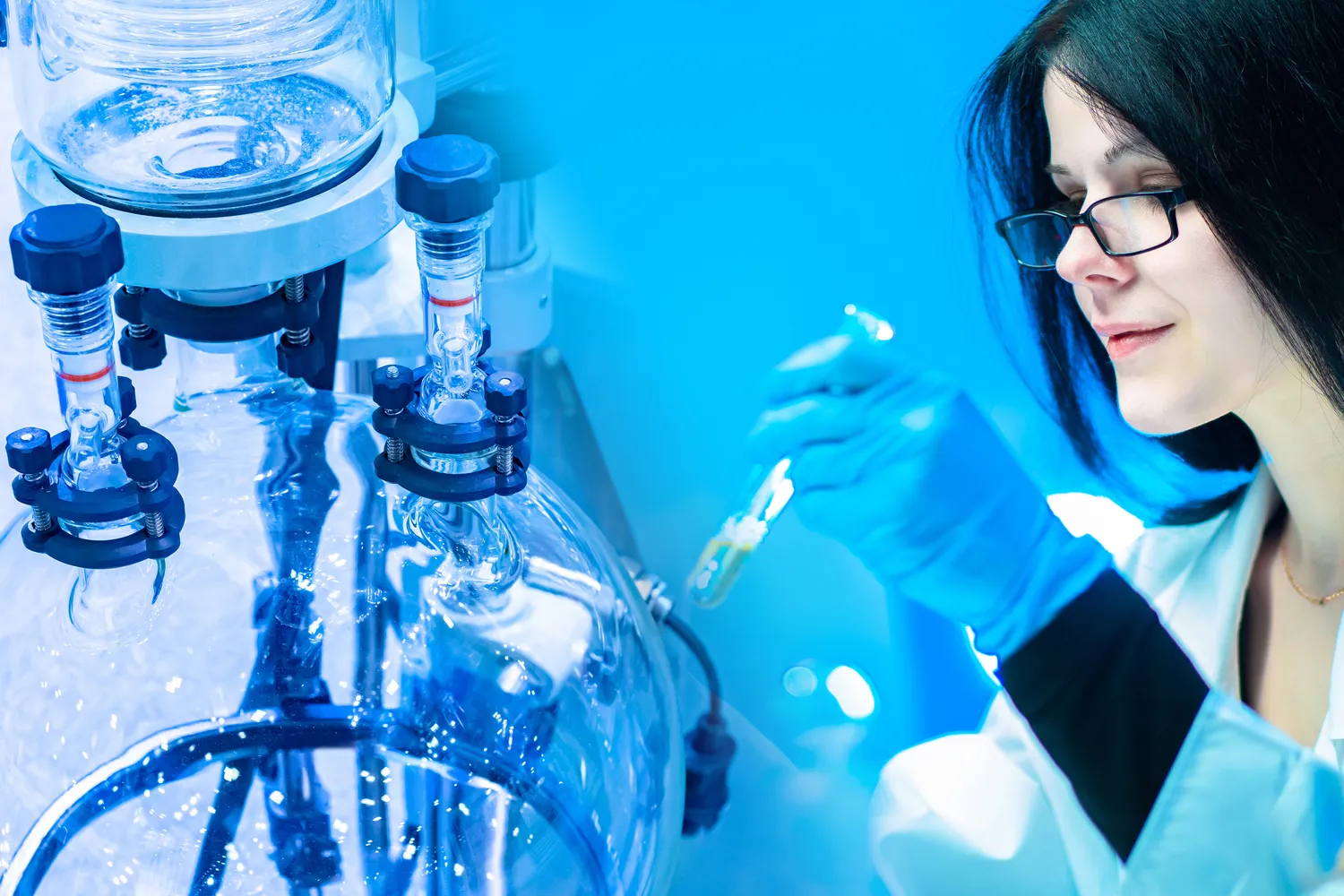
Destylacja rozpuszczalników ma wiele zalet, które sprawiają, że jest to popularna metoda separacji w różnych branżach. Przede wszystkim pozwala na uzyskanie wysokiej czystości produktów końcowych, co jest kluczowe w przemyśle farmaceutycznym oraz chemicznym. Proces ten jest również stosunkowo prosty do zautomatyzowania i skalowania, co ułatwia jego wdrożenie w dużych zakładach produkcyjnych. Dodatkowo destylacja nie wymaga użycia agresywnych reagentów chemicznych, co czyni ją bezpieczną metodą separacji. Niemniej jednak istnieją także pewne ograniczenia związane z tą techniką. Jednym z głównych wyzwań jest konieczność precyzyjnego kontrolowania warunków procesu, ponieważ niewłaściwe ustawienia mogą prowadzić do nieefektywnej separacji lub degradacji składników. Ponadto niektóre mieszaniny mogą tworzyć azeotropy, co utrudnia ich dalsze oczyszczanie.
Jakie są zastosowania destylacji rozpuszczalników w przemyśle
Destylacja rozpuszczalników znajduje szerokie zastosowanie w różnych gałęziach przemysłu ze względu na swoją efektywność i możliwość uzyskania wysokiej czystości produktów. W przemyśle chemicznym proces ten jest kluczowy dla produkcji wielu substancji chemicznych oraz ich oczyszczania. Na przykład w produkcji alkoholi etylowych destylacja pozwala na oddzielenie etanolu od innych składników fermentacyjnych. W przemyśle farmaceutycznym natomiast stosuje się ją do oczyszczania substancji czynnych oraz rozpuszczalników używanych w syntezach chemicznych. Również przemysł petrochemiczny korzysta z tej metody do separacji frakcji ropy naftowej, takich jak benzyna czy oleje napędowe. W laboratoriach badawczych destylacja służy do przygotowywania czystych reagentów oraz analizy składów chemicznych próbek.
Jakie są najważniejsze czynniki wpływające na destylację rozpuszczalników
W procesie destylacji rozpuszczalników istnieje wiele czynników, które mogą znacząco wpłynąć na jego efektywność i jakość uzyskanego produktu. Kluczowym elementem jest temperatura, która musi być precyzyjnie kontrolowana, aby zapewnić odpowiednie warunki do parowania i skraplania. Zbyt wysoka temperatura może prowadzić do degradacji składników, natomiast zbyt niska może skutkować niepełnym oddzieleniem substancji. Kolejnym istotnym czynnikiem jest ciśnienie atmosferyczne, które wpływa na temperatury wrzenia substancji. W przypadku destylacji podciśnieniowej obniżenie ciśnienia pozwala na przeprowadzenie procesu w niższej temperaturze, co jest korzystne dla substancji wrażliwych na wysoką temperaturę. Również rodzaj używanego sprzętu ma znaczenie; kolumny destylacyjne o odpowiedniej konstrukcji mogą zwiększyć efektywność separacji poprzez umożliwienie wielokrotnego skraplania i parowania.
Jakie są różnice między destylacją a innymi metodami separacji
Destylacja rozpuszczalników jest jedną z wielu metod separacji stosowanych w przemyśle i laboratoriach, a jej skuteczność często porównywana jest z innymi technikami, takimi jak ekstrakcja czy chromatografia. W przeciwieństwie do ekstrakcji, która polega na przenoszeniu składników z jednej fazy do drugiej na podstawie ich rozpuszczalności, destylacja opiera się na różnicy temperatur wrzenia składników. To sprawia, że destylacja jest bardziej odpowiednia dla mieszanin cieczy, gdzie składniki mają wyraźnie różniące się temperatury wrzenia. Z kolei chromatografia to technika separacyjna oparta na różnicach w adsorpcji lub rozpuszczalności składników w różnych fazach. Jest ona szczególnie przydatna w analizach jakościowych i ilościowych oraz w przypadku bardzo skomplikowanych mieszanin. Warto również zauważyć, że podczas gdy destylacja jest procesem fizycznym, inne metody separacji mogą wykorzystywać reakcje chemiczne lub interakcje molekularne.
Jakie są najczęstsze błędy popełniane podczas destylacji rozpuszczalników
Podczas przeprowadzania destylacji rozpuszczalników można napotkać wiele pułapek i błędów, które mogą prowadzić do nieefektywności procesu lub obniżenia jakości uzyskanego produktu. Jednym z najczęstszych błędów jest niewłaściwe ustawienie temperatury grzania. Zbyt szybkie podgrzewanie cieczy może prowadzić do niekontrolowanego parowania i utraty cennych składników, a także do powstawania niepożądanych produktów ubocznych. Innym problemem może być niewłaściwe dobranie sprzętu; użycie kolumny destylacyjnej o niewłaściwej konstrukcji lub średnicy może ograniczyć efektywność separacji. Ponadto brak odpowiedniej kontroli ciśnienia może prowadzić do trudności w osiągnięciu optymalnych warunków dla danego procesu. Warto również zwrócić uwagę na czystość używanych materiałów; zanieczyszczone rozpuszczalniki mogą wpływać na wyniki destylacji i prowadzić do kontaminacji końcowego produktu.
Jakie są nowoczesne technologie wspierające proces destylacji rozpuszczalników
W ostatnich latach rozwój technologii znacząco wpłynął na proces destylacji rozpuszczalników, wprowadzając nowe metody i urządzenia mające na celu zwiększenie efektywności oraz bezpieczeństwa tego procesu. Jednym z przykładów są systemy destylacyjne oparte na technologii membranowej, które pozwalają na separację składników bez konieczności podgrzewania cieczy. Dzięki temu możliwe jest oszczędzanie energii oraz minimalizacja ryzyka degradacji termicznej substancji. Kolejną nowoczesną technologią jest destylacja podciśnieniowa, która umożliwia przeprowadzanie procesu w niższych temperaturach dzięki obniżeniu ciśnienia atmosferycznego. To podejście jest szczególnie korzystne dla substancji wrażliwych na wysoką temperaturę oraz dla mieszanin zawierających lotne składniki. Dodatkowo automatyzacja procesów destylacyjnych za pomocą zaawansowanych systemów sterowania pozwala na precyzyjne monitorowanie warunków pracy oraz optymalizację parametrów procesu w czasie rzeczywistym.
Jakie są przyszłe kierunki rozwoju technologii destylacji rozpuszczalników
Przyszłość technologii destylacji rozpuszczalników wydaje się obiecująca dzięki ciągłemu postępowi naukowemu oraz rosnącemu zapotrzebowaniu na bardziej efektywne i ekologiczne metody separacji. W kontekście zmian klimatycznych oraz rosnącej świadomości ekologicznej przemysł chemiczny stara się wdrażać technologie zmniejszające zużycie energii oraz minimalizujące odpady produkcyjne. Jednym z kierunków rozwoju jest poszukiwanie alternatywnych metod separacji opartych na wykorzystaniu energii odnawialnej lub procesach biotechnologicznych. Ponadto rozwój nanotechnologii otwiera nowe możliwości w zakresie projektowania materiałów filtracyjnych o wyjątkowych właściwościach adsorpcyjnych, co może zrewolucjonizować tradycyjne metody destylacyjne. W miarę jak technologia będzie się rozwijać, można spodziewać się coraz większej integracji różnych metod separacyjnych w celu osiągnięcia lepszych wyników przy niższych kosztach operacyjnych.
Jakie są najważniejsze aspekty bezpieczeństwa w destylacji rozpuszczalników
Bezpieczeństwo w procesie destylacji rozpuszczalników jest kluczowym zagadnieniem, które wymaga szczególnej uwagi ze względu na potencjalne zagrożenia związane z obsługą substancji chemicznych oraz wysokimi temperaturami. Przede wszystkim istotne jest stosowanie odpowiednich środków ochrony osobistej, takich jak rękawice, gogle czy odzież ochronna, aby zminimalizować ryzyko kontaktu z niebezpiecznymi substancjami. Ważne jest również, aby wszystkie urządzenia były regularnie kontrolowane i konserwowane, co pozwala na uniknięcie awarii oraz wycieków. W przypadku pracy z łatwopalnymi rozpuszczalnikami należy zapewnić odpowiednią wentylację oraz unikać źródeł zapłonu w pobliżu miejsca pracy. Dodatkowo, warto wdrożyć procedury awaryjne oraz szkolenia dla personelu, aby każdy był przygotowany na ewentualne sytuacje kryzysowe.