Destylator laboratoryjny to urządzenie wykorzystywane w chemii do separacji substancji na podstawie różnic w ich temperaturach wrzenia. Działa na zasadzie podgrzewania cieczy, co powoduje jej odparowanie, a następnie skraplanie pary w celu uzyskania czystego produktu. W laboratoriach destylatory są niezbędne do oczyszczania rozpuszczalników, ekstrakcji związków chemicznych oraz analizy składników mieszanin. Proces destylacji może być przeprowadzany w różnych warunkach, takich jak destylacja prosta, frakcyjna czy też próżniowa, co pozwala na dostosowanie metody do specyfiki badanej substancji. W przypadku destylacji frakcyjnej wykorzystuje się kolumny frakcyjne, które zwiększają efektywność oddzielania składników poprzez wielokrotne skraplanie i odparowywanie. Destylatory laboratoryjne mogą mieć różne rozmiary i kształty, a ich konstrukcja często obejmuje elementy takie jak balon destylacyjny, chłodnica oraz zbiornik na skropliny.
Jakie są rodzaje destylatorów laboratoryjnych i ich zastosowania
W laboratoriach można spotkać kilka rodzajów destylatorów, z których każdy ma swoje specyficzne zastosowanie. Najpopularniejszym typem jest destylator prosty, który składa się z balonu destylacyjnego oraz chłodnicy. Używa się go głównie do oczyszczania cieczy o znacznej różnicy temperatur wrzenia. Kolejnym rodzajem jest destylator frakcyjny, który jest bardziej zaawansowany i umożliwia separację składników o zbliżonych temperaturach wrzenia dzięki zastosowaniu kolumny frakcyjnej. Tego typu urządzenie jest szczególnie przydatne w przemyśle petrochemicznym oraz w produkcji alkoholi. Istnieją także destylatory próżniowe, które działają w obniżonym ciśnieniu, co pozwala na destylację substancji w niższych temperaturach. To rozwiązanie jest idealne dla substancji termolabilnych, które mogą ulegać degradacji w wysokich temperaturach. Warto również wspomnieć o destylatorach azeotropowych, które umożliwiają oddzielanie składników tworzących azeotropy, czyli mieszaniny o stałym składzie.
Jakie materiały są używane do budowy destylatorów laboratoryjnych
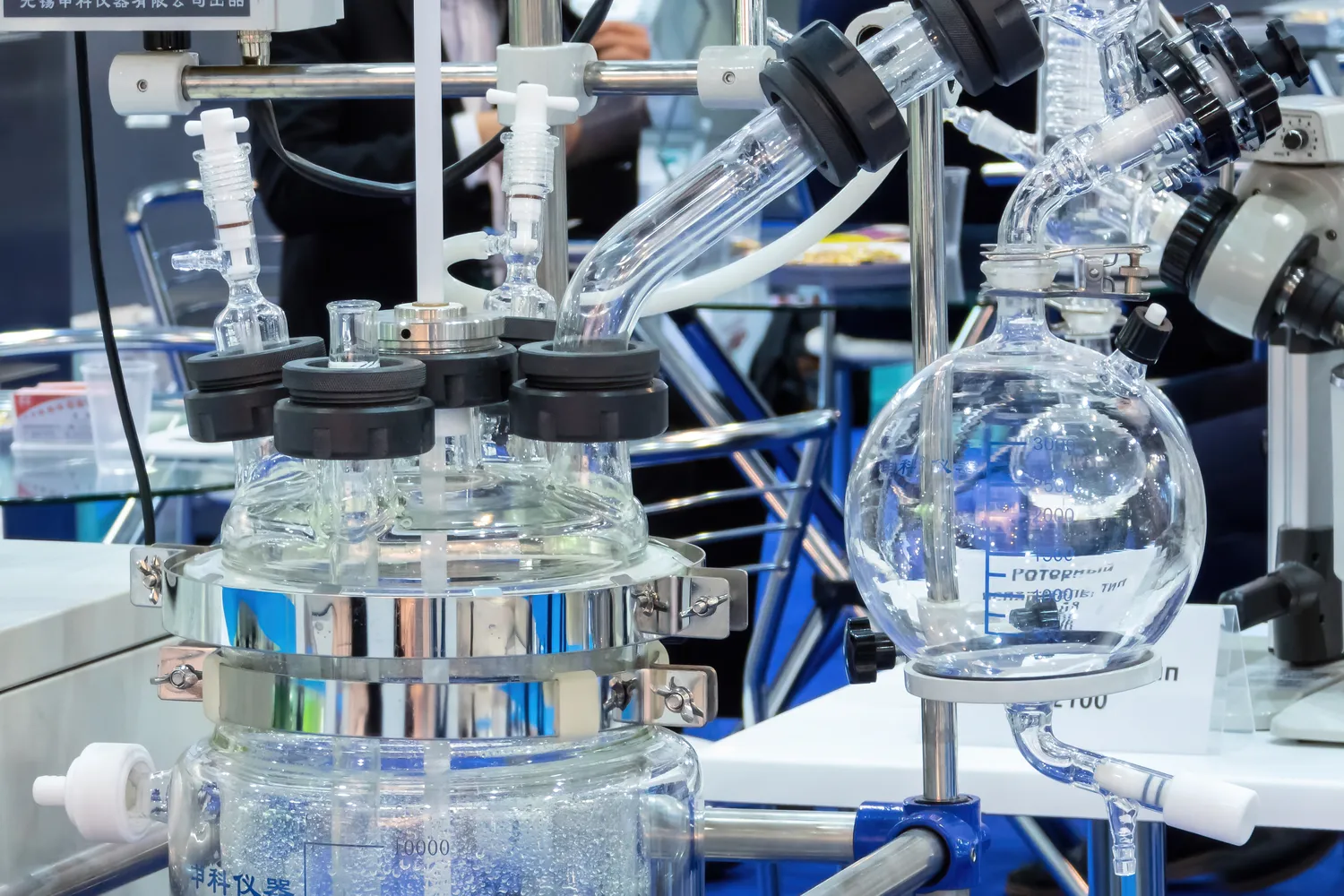
Budowa destylatora laboratoryjnego wymaga zastosowania odpowiednich materiałów, które zapewnią nie tylko trwałość urządzenia, ale także jego bezpieczeństwo podczas pracy. Najczęściej stosowanym materiałem jest szkło borokrzemowe, które charakteryzuje się wysoką odpornością na zmiany temperatury oraz chemikalia. Szkło to jest idealne do budowy balonów destylacyjnych oraz chłodnic, ponieważ nie reaguje z większością substancji chemicznych. W przypadku elementów narażonych na wysokie ciśnienie lub intensywne użytkowanie można zastosować stal nierdzewną lub inne metale odporne na korozję. Ważnym aspektem jest również uszczelnienie połączeń między poszczególnymi elementami urządzenia. Do tego celu często wykorzystuje się gumowe lub silikonowe uszczelki, które zapewniają szczelność systemu i minimalizują ryzyko wycieków substancji chemicznych. Oprócz tego istotnym elementem są również termometry oraz manometry, które umożliwiają monitorowanie warunków pracy destylatora.
Jakie są najważniejsze zalety korzystania z destylatora laboratoryjnego
Korzystanie z destylatora laboratoryjnego niesie ze sobą wiele korzyści zarówno dla naukowców, jak i dla przemysłu chemicznego. Przede wszystkim umożliwia on uzyskanie wysokiej czystości substancji poprzez skuteczną separację składników mieszanin. Dzięki temu można otrzymać czyste rozpuszczalniki czy też wyizolować pożądane związki chemiczne do dalszych badań lub produkcji. Destylacja jest także procesem stosunkowo prostym i łatwym do kontrolowania, co sprawia, że można go dostosować do różnych potrzeb badawczych czy produkcyjnych. Kolejną zaletą jest możliwość wielokrotnego wykorzystania tego samego sprzętu do różnych procesów chemicznych, co obniża koszty operacyjne laboratorium. Ponadto nowoczesne destylatory często wyposażone są w zaawansowane systemy monitorujące i automatyzujące procesy, co zwiększa ich wydajność i precyzję działania.
Jakie są najczęstsze błędy przy używaniu destylatorów laboratoryjnych
Przy pracy z destylatorami laboratoryjnymi, nawet drobne błędy mogą prowadzić do nieefektywności procesu lub, co gorsza, do niebezpiecznych sytuacji. Jednym z najczęstszych błędów jest niewłaściwe ustawienie temperatury podgrzewania. Zbyt wysoka temperatura może prowadzić do przegrzewania substancji, co z kolei może skutkować ich rozkładem lub powstawaniem niepożądanych produktów ubocznych. Ważne jest również, aby dostosować tempo podgrzewania do rodzaju substancji i jej właściwości fizykochemicznych. Kolejnym powszechnym błędem jest niedostateczne uszczelnienie połączeń między elementami destylatora. Nieszczelności mogą prowadzić do utraty cennych składników oraz zwiększać ryzyko wybuchu pary. Użytkownicy często zapominają także o regularnym czyszczeniu i konserwacji urządzenia, co może prowadzić do osadzania się zanieczyszczeń i obniżenia efektywności destylacji. Należy również pamiętać o odpowiednim chłodzeniu skroplin, ponieważ niewłaściwe warunki mogą wpłynąć na jakość uzyskiwanego produktu.
Jakie są koszty zakupu destylatora laboratoryjnego
Koszt zakupu destylatora laboratoryjnego może się znacznie różnić w zależności od jego typu, wielkości oraz dodatkowych funkcji. Proste destylatory szklane, które są podstawowym wyposażeniem wielu laboratoriów, można nabyć już za kilkaset złotych. Jednak bardziej zaawansowane modele, takie jak destylatory frakcyjne czy próżniowe, mogą kosztować kilka tysięcy złotych. W przypadku dużych instalacji przemysłowych ceny mogą sięgać dziesiątek tysięcy złotych. Oprócz samego urządzenia warto również uwzględnić dodatkowe koszty związane z akcesoriami, takimi jak kolumny frakcyjne, chłodnice czy termometry. Koszty eksploatacji również powinny być brane pod uwagę; obejmują one zużycie energii elektrycznej, konserwację oraz ewentualne naprawy. Warto także rozważyć zakup używanego sprzętu, który często można znaleźć w dobrym stanie w przystępnych cenach.
Jakie są zastosowania destylatorów laboratoryjnych w różnych branżach
Destylatory laboratoryjne znajdują szerokie zastosowanie w różnych branżach przemysłu oraz nauki. W przemyśle chemicznym są one wykorzystywane do oczyszczania surowców oraz produkcji chemikaliów o wysokiej czystości. Przykładem mogą być procesy produkcji alkoholi, gdzie destylacja jest kluczowym etapem w uzyskiwaniu czystych etanolów czy innych związków organicznych. W laboratoriach analitycznych destylatory służą do separacji składników mieszanin w celu przeprowadzenia dalszych badań i analiz jakościowych. W branży farmaceutycznej wykorzystuje się je do produkcji leków oraz substancji czynnych, gdzie czystość i jakość składników mają kluczowe znaczenie dla skuteczności terapii. Destylatory znajdują również zastosowanie w biotechnologii, gdzie są wykorzystywane do ekstrakcji bioaktywnych związków z roślin czy mikroorganizmów. Również w przemyśle spożywczym destylacja odgrywa istotną rolę w produkcji olejków eterycznych oraz aromatów.
Jakie innowacje technologiczne wpływają na rozwój destylatorów laboratoryjnych
W ostatnich latach obserwuje się dynamiczny rozwój technologii związanych z destylatorami laboratoryjnymi, co przekłada się na ich wydajność i funkcjonalność. Nowoczesne destylatory często wyposażone są w systemy automatyzacji, które umożliwiają precyzyjne kontrolowanie parametrów procesu destylacji, takich jak temperatura czy ciśnienie. Dzięki temu użytkownicy mogą osiągnąć lepsze wyniki oraz zmniejszyć ryzyko błędów ludzkich. Innowacyjne materiały używane do budowy destylatorów pozwalają na zwiększenie ich odporności na korozję oraz wysokie temperatury, co wydłuża żywotność urządzeń. Wprowadzenie inteligentnych systemów monitorujących umożliwia zdalne zarządzanie procesem oraz bieżące śledzenie jego parametrów przez aplikacje mobilne lub komputery stacjonarne. Ponadto rozwój technologii próżniowej pozwala na efektywniejszą separację składników o niskich temperaturach wrzenia bez ryzyka ich degradacji. Warto również zauważyć rosnące zainteresowanie ekologicznymi rozwiązaniami w procesie destylacji, takimi jak odzysk energii czy minimalizacja odpadów chemicznych.
Jakie są zasady bezpieczeństwa przy pracy z destylatorami laboratoryjnymi
Praca z destylatorami laboratoryjnymi wiąże się z pewnym ryzykiem, dlatego przestrzeganie zasad bezpieczeństwa jest niezwykle istotne dla ochrony zdrowia użytkowników oraz środowiska. Przede wszystkim należy zawsze stosować odpowiednie środki ochrony osobistej, takie jak okulary ochronne, rękawice chemiczne oraz fartuchy laboratoryjne. Ważne jest również zapewnienie odpowiedniej wentylacji w pomieszczeniu roboczym, aby uniknąć gromadzenia się szkodliwych par czy oparów chemicznych. Użytkownicy powinni być świadomi potencjalnych zagrożeń związanych z substancjami chemicznymi używanymi w procesie destylacji i znać procedury postępowania w przypadku awarii lub wycieku substancji. Regularna konserwacja i inspekcja sprzętu to kolejny kluczowy element zapewnienia bezpieczeństwa; wszelkie uszkodzenia powinny być natychmiast naprawiane lub zgłaszane odpowiednim służbom technicznym. Należy także pamiętać o odpowiednim oznakowaniu substancji chemicznych oraz przestrzeganiu zasad BHP dotyczących ich przechowywania i transportu.
Jakie są przyszłe kierunki rozwoju technologii destylacyjnej
Przyszłość technologii destylacyjnej zapowiada się obiecująco dzięki ciągłemu rozwojowi nauki i technologii. Jednym z głównych kierunków rozwoju jest dążenie do zwiększenia efektywności energetycznej procesów distylacyjnych poprzez zastosowanie nowoczesnych materiałów izolacyjnych oraz systemów odzysku ciepła. W miarę wzrostu świadomości ekologicznej coraz większą uwagę przykłada się do minimalizacji odpadów chemicznych oraz optymalizacji procesów produkcyjnych w celu zmniejszenia ich wpływu na środowisko naturalne. Rozwój technologii cyfrowej otwiera nowe możliwości automatyzacji i monitorowania procesów distylacyjnych za pomocą sztucznej inteligencji oraz analizy danych w czasie rzeczywistym. To pozwala na lepsze dostosowanie parametrów procesu do zmieniających się warunków i potrzeb użytkowników. Kolejnym interesującym kierunkiem jest rozwój metod ekstrakcji cieczy nadkrytycznych jako alternatywy dla tradycyjnej distylacji, co może przyczynić się do uzyskania wyższej jakości produktów końcowych przy mniejszym zużyciu energii i czasu.